After the customer approves the samples and places the PO, engineering department, production department and quality department will get together to discuss production transfer issues. Engineering department and quality department will transfer standard operation procedure (SOP), injection molding conditions and inspection instructions to production department. Production department prepares the production schedule according to the PO and current workload. Theabove three departments will jointly organize operators and inspectors for trainings.
We’re equipped with injection molding machines with tonnage from 60T to 600T and injection volume from 35g to 2000g. In order to ensure their normal conditions and uses, molds and machines are maintained, and operators and inspectors are trained on a regular basis. Prior to starting machine to mold, quality inspectors will point check machines and molds. When the molding is stable, quality inspectors will sign for first articles according to inspection instructions and customer-approved samples and carry out process inspection and final inspection. Once noticing a quality problem, inspectors will inform the lead of operators to stop the machine. After the problem is analyzed and corrected, production resumes.
Over the years we have used many different types of plastics, including conventional resins of PP, PE, PS, ABS, nylon, POM, acrylic, PVC, and PC, as well as engineering resins of PVDF, PEI, PES, and PEEK.
We have accumulated lots of practical experience about the molding conditions and process tunings of different materials.
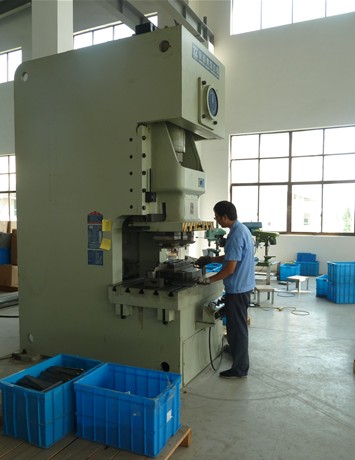